Value Stream Mapping (VSM) – Helping understand the big picture
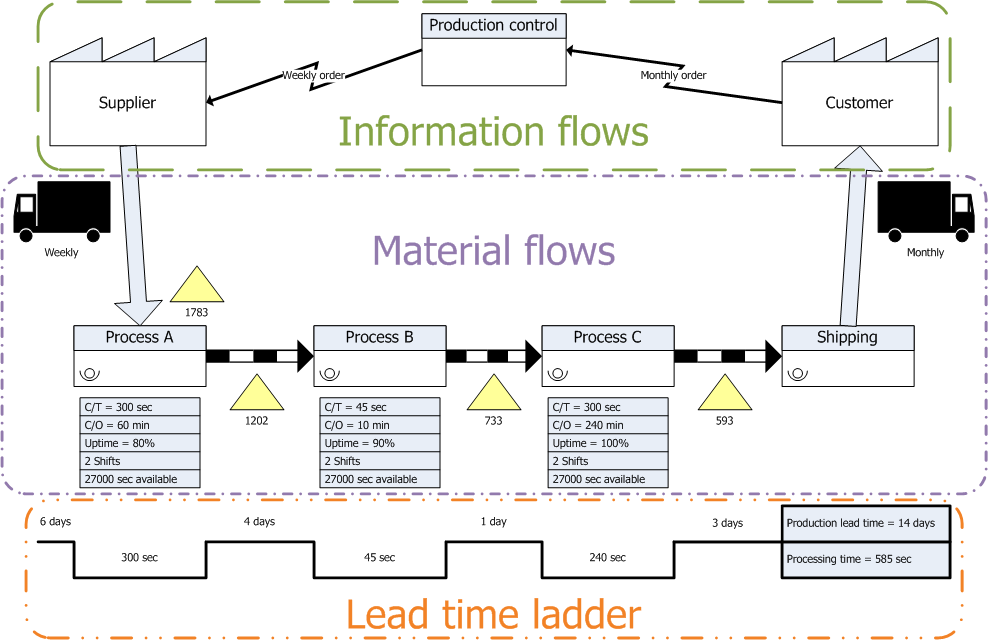
Oftentimes during improvement projects, one is so focussed on solving the direct problem or improving the local situation, that one fails to understand the impact of the change on the up- or downstream process. This could mean creating a local optima without consideration of, or worse, to the detriment of, the global optimum. There is often a misconception that the sum of local optima will lead to an even greater global optimum. Unfortunately, this is not always true.
This is where the Value Stream Map (VSM) really comes into its own as a powerful tool in the Operational Excellence toolbox. It helps to represent the flow of material and information through the entire process. As such it is useful in understanding flows, queues, and bottlenecks.
Understanding Value Stream Mapping
Value Stream Mapping is a visual and analytical tool that enables organizations to create a detailed, end-to-end view of their processes. It involves mapping the flow of materials, information, and actions required to deliver a product or service to the customer. VSM provides a holistic perspective on how value is created, and it identifies areas where improvements can be made to eliminate non-value-added activities or waste. It helps identifying where small changes could have the biggest overall effect.
Why spend the time to create a Value Stream Mapping
VSM is a versatile tool to map virtually any process. Value Stream Mapping offers several benefits:
- Waste Reduction: VSM helps identify and eliminate waste, leading to cost savings and improved efficiency.
- Improved Quality: By streamlining processes and reducing defects, VSM contributes to higher product and service quality.
- Enhanced Customer Satisfaction: Delivering value more efficiently often results in faster delivery times and better customer service.
- Cost Savings: VSM can lead to significant cost reductions by optimizing resource utilization and minimizing waste.
- Employee Engagement: Involving employees in VSM activities fosters a culture of continuous improvement, increasing employee satisfaction and retention.
- Collaboration: VSM facilitate collaboration an communication. They are also transferable by transferring lessons learned in one area of the business to other areas.
- Competitive Advantage: Organizations that embrace VSM gain a competitive edge by being more agile and responsive to customer needs.
- Value for Money: Creating a VSM is inexpensive and easy! If digitized it can be used as a (high level) model to play out various what-if scenarios. As such it can be an excellent strategy tool as well as an emergency response tool.
Key Value Stream Mapping Activities
- Selecting the Value Stream: The first step in VSM involves choosing a specific value stream to analyze. This could be a particular product line, service, or process within the organization.
- Creating a Current State Map: This activity involves creating a visual representation of the current state of the selected value stream. It includes capturing data on process steps, cycle times, inventory levels, and other relevant metrics. This map serves as a baseline for improvement efforts.
- Identifying Waste: VSM activities aim to identify and categorize different types of waste, such as overproduction, waiting times, excess inventory, and defects. Recognizing waste is essential for prioritizing improvement opportunities.
- Developing a Future State Map: After analyzing the current state, VSM practitioners create a future state map that outlines the ideal flow of value within the value stream. This map is designed to eliminate waste and optimize processes.
- Gap Analysis: A crucial activity in VSM is the gap analysis, which compares the current state and future state maps to identify the differences. These gaps represent the areas that require improvement and serve as the foundation for action plans.
- Implementing Improvements: Based on the gap analysis, organizations can develop action plans to implement improvements in the value stream. These improvements may include process changes, technology enhancements, or workflow optimizations.
- Continual Monitoring and Review: VSM is not a one-time exercise; it is an ongoing process of continuous improvement. Regularly monitoring the value stream and comparing it to the future state map helps organizations sustain gains and make further enhancements.
And now?
Value Stream Mapping activities play a vital role in helping organizations improve their processes, reduce waste, and enhance efficiency. By identifying opportunities for improvement and implementing changes, businesses can achieve higher quality, lower costs, and improved customer satisfaction. VSM is not just a one-time endeavor but a continuous journey towards excellence, ensuring that organizations remain competitive and adaptable in today’s dynamic business environment.
Kallion’s approach can be tailored to virtually any laboratory. Our experts can help map processes, identify improvement levers and quantifying their impact and therefore help prioritize corrective and preventative actions. Kallion can customize its consulting support to assist the laboratory with the successful and sustained roll-out of these actions. Please reach out for an initial discussion on how Kallion can assist you.