Why do Operational Excellence Initiatives Fail?
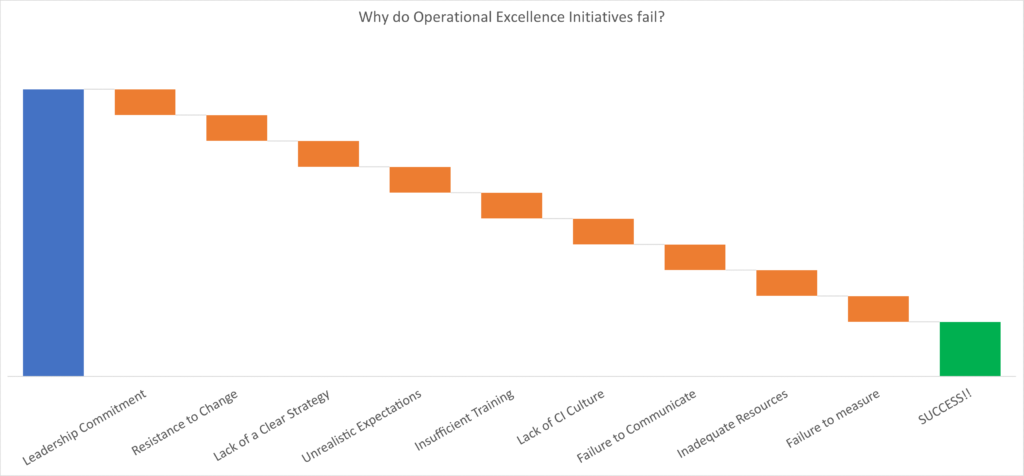
Operational Excellence projects are designed to streamline processes, enhance efficiency, and optimize overall business performance. However, despite their noble intentions, these initiatives don’t always yield the expected results. So: why do Operational Excellence initiatives fail?
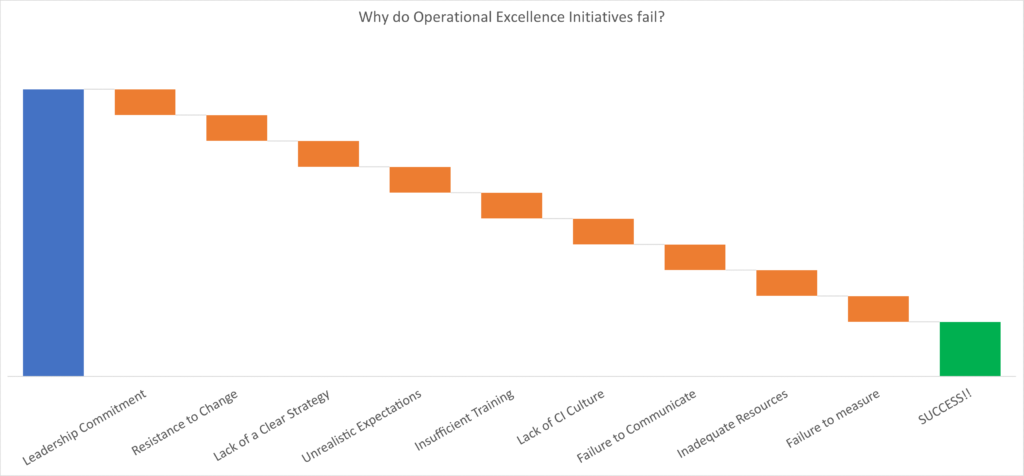
Inadequate Leadership Commitment
One of the primary reasons Operational Excellence projects hit roadblocks is the lack of unwavering commitment from top leadership. When executives fail to champion the cause, the entire organization may struggle to embrace the necessary changes. A successful OpEx implementation requires leaders who not only endorse the initiative but actively participate and communicate its importance throughout the organization.
Resistance to Change
Human nature tends to resist change, and organizations are no exception. Employees may be resistant to altering established routines. This in turn leads to a lack of enthusiasm and cooperation during the implementation of Operational Excellence initiatives. Overcoming this resistance requires a robust change management strategy. That strategy involves communication, training, and engagement at all levels of the organization.
Lack of a Clear Strategy
The absence of a well-defined strategy is a critical factor contributing to the failure of Operational Excellence projects. Organizations need a clear roadmap outlining how the Operational Excellence initiative aligns with overall business goals, the specific processes targeted for improvement, and the expected outcomes. Without a strategic framework, efforts may lack direction, leading to confusion and ineffective implementation.
Unrealistic Expectations
Setting unrealistic goals and expectations can doom Operational Excellence projects from the outset. Organizations must establish achievable milestones and objectives, considering the unique challenges and capabilities of their workforce. Unrealistic expectations can lead to frustration, loss of morale, and a perception that the initiative is unattainable, ultimately resulting in project failure.
Insufficient Training and Development
Successful implementation of Operational Excellence requires a well-trained and capable workforce. Inadequate training programs can hinder employees’ ability to adapt to new processes and technologies, leading to inefficiencies and errors. Organizations must invest in comprehensive training and development initiatives to ensure that employees are equipped with the necessary skills to thrive in the evolving operational landscape.
Lack of Continuous Improvement Culture
Operational Excellence is an ongoing journey, not a one-time destination. Organizations that view Operational Excellence as a short-term project rather than a continuous improvement culture are destined to encounter challenges. Sustainable success requires fostering a culture of continuous improvement, where employees are encouraged to identify and address inefficiencies on an ongoing basis.
Failure to Communicate
Throughout the transformation, communication in various forms are needed to keep staff engaged. At the start the reason for change is a key part of the narrative. During the implementation phase, continuously communicating successes (and challenges) keeps staff involved and informed. A failure to communicate may therefore cause staff to become disenfranchised and disconnected.
Inadequate Resources
Performing an analysis of how processes can be improved and brainstorming solutions require time while implementing improvement ideas may require investment, new equipment, changes in IT systems, etc. A failure to provide adequate resources, not only in money but also of time, is thus a sure way to ensure that a transformation will not be a success.
Conclusion
While Operational Excellence projects hold the promise of transforming organizations, their success is contingent on careful planning, commitment, and a keen understanding of potential pitfalls. By addressing issues listed above, organizations can navigate the complexities of OpEx implementation and increase the likelihood of achieving lasting success.
Kallion can assist and support laboratories on their journey to successful Operational Excellence roll-out. Kallion’s training, diagnostic approach and implementation support can be tailored to virtually any kind of laboratories. Please reach out for an initial discussion on how Kallion can assist you or to share with us your views on why Operational Excellence initiatives fail?