Simple. Spectacular. Spotless. Systematized. Sustainable. No, these are not the steps of 5S, but they do describe the methodology and it’s affects quite well. 5S represents a way of working which assigns a place for everything and makes sure everything is in place. 5S, simple yet powerful.
What are the 5S?
- Sort (Seiri) – In the first step items in the workplace are sorted the based on use. By simply asking: “Is the item used?” one can determine whether the item can be removed from the workspace through (safe) disposal, donation, sale or whether the item should be kept.
- Set in order (Seiton) – Remaining items are assigned a dedicated location based on the frequency of their use with items used frequently e.g. daily being placed conveniently within reach. Items used weekly or monthly are placed on upper or lower shelves or in cupboards in a central location while items that are used less frequently can be placed at some distance from the daily workspace e.g. in the warehouse.
- Shine (Seisō) – Items are now thoroughly cleaned, and a system designed to ensure that items remain clean. This means that:
- Items are returned to their fundamental, original condition. This can be done by (either partially or completely) taking items apart and giving a thorough cleaning.
- The process, items or surroundings are adapted to avoid the item or workspace from becoming dirty again in the future. Installing a drip tray to avoid leaks is an example.
- The process item or surroundings can also be adjusted to make future cleaning easier and more effective if needed. Lifting items of the floor can facilitate future cleaning of a workspace for example.
- Standardize (Seiketsu) – The help maintain the new way of working, the work processes or work items should be standardized through labelling, colour coding, error proofing (Poka Yoke) or, if needed, complete redesign.
- Sustain (Shitsuke) – Quite simply, the last step of 5S aims to ensure that the improvements made becomes permanent and institutionalized to ensure that the benefits are not lost.
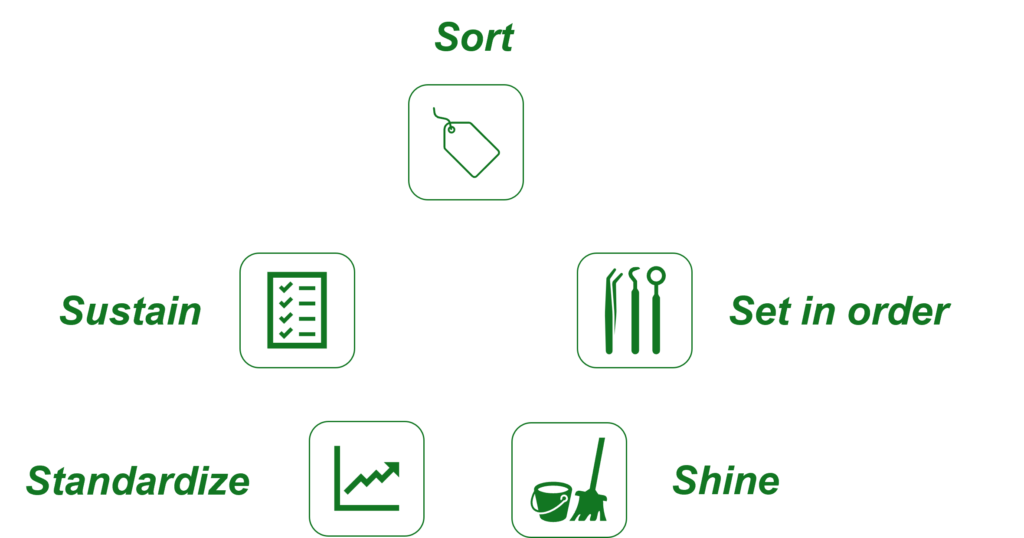
Why bother?
There are innumerable benefits to the roll-out of a 5S culture in a workspace. Some of the most significant benefits include:
- Health and Safety of staff is improved because of standardized, uncluttered workspaces.
- Quality is improved because work is clear and standardized and errors are reduced or avoided.
- Productivity is increased because employees spend less time looking for work items or correcting errors.
- Processing times are improved.
- The amount of workspace required for certain activities are reduced.
- Inventory, and thus working capital, can be kept to a minimum.
- The workplace looks great! Not only for staff, creating a comfortable and enjoyable work environment, but also for the customer, thus creating a professional and trusting image in the eye of the customer.
What about 6S?
Often called 5S plus Safety, 6S is a modern take on 5S that aim to ensure that safety is considered in the decision making process during the implementation of 5S.
How we Kallion help
Kallion’s diagnostic and support approach can be tailored to virtually any laboratory and can help to identify the areas in the process where 5S would be most helpful. The consulting support offered by Kallion can further be customized to assist the laboratory with the successful and sustained roll-out of an effective 5S culture. Please reach out for an initial discussion on how Kallion can assist you.