(Lean) waste in laboratories
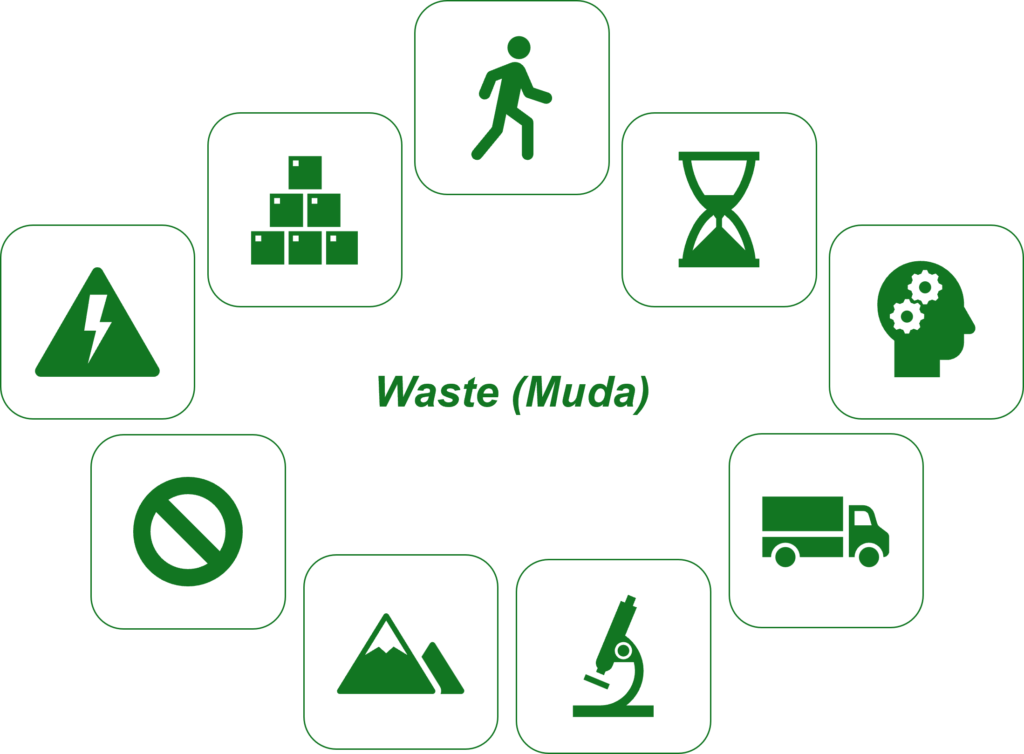
What is it and why should we care
The birthplace of Lean is industry. This means that for a long time, the focus has been on manufacturing, processing, and other aspects of business where machines and equipment take a central role. In recent years there has been advances in other sectors with great work in hospitals for example. The service related industries, in which staff time constitute the main production asset are progressively deploying lean methodologies. But even here the laboratories have often been left behind. If we were to shine a spotlight on any laboratory, we will however find that (lean) waste is omnipresent. The question is what would these wastes be in laboratories and why should we care?
The 8 (or is it 9?) wastes and their impact
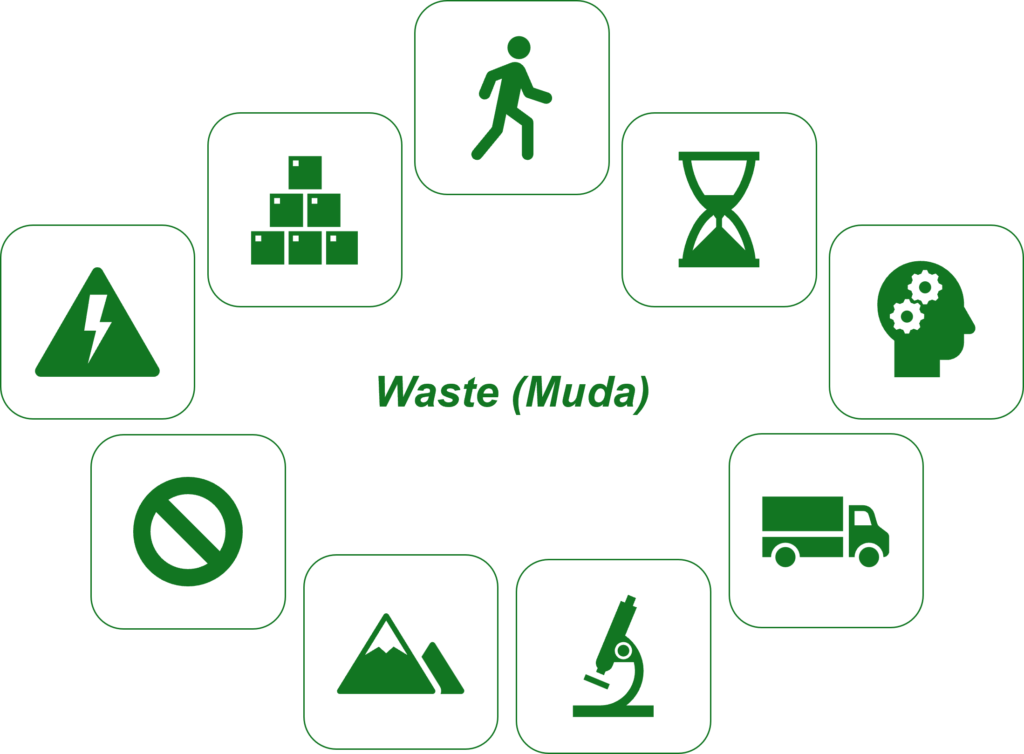
- Ineffectual use of the time, skills, ideas, or capacity of staff (and equipment) does not only cause staff to become disheartened but also lead to losses in output capacity which in turn affects the service a laboratory can offer to a customer.
- Delays due to the previous or next activity causes waiting and increases lead times.
- A build-up of items or work in progress kept beyond acceptable process limits leads to excessive inventory levels. This not only locks working capital in the process but also increases cost and could lead to mistakes. Inventory is often seen as the mother of all other wastes.
- Any motion (incl. non-ergonomic movement) not needed to perform a task means that laboratories are not using our most vital resource, their skilled and motivated staff, to do what they do best.
- Overprocessing of items by performing more work than required not only means that there is an excessive consumption of resources which adds cost but also leads to losses in lead time and capacity.
- The non-essential transport of items leads to longer lead times, extra cost, and potential quality issues.
- By producing more items than the process or customer requires we incur extra cost. It can be for example through storage and disposal of unused or expired goods. It can also be through unrequired duplicate analysis. Overproduction is not very common in laboratories and therefore easy to miss or dismiss. It is however the worst type of waste as it induces most of the other ones.
- Failing to meet the customer requirements, creating defects or performing rework all affect the quality of the service a laboratory offers to customers. The long-term cost of poor quality does not often reflect in the bottom line. However in the long run it could be disastrous to a laboratory.
- Energy that is not usefully transferred, transformed or utilized once generated not only increases cost but could deteriorate a laboratory’s reputation.
What can you do about waste?
There is a plethora of tools to potentially use to tackle, reduce and even eliminate (lean) waste in laboratories. These could range from fully automated analysers and advanced ERPs to visual management, standardized work and 5S. Sometimes knowing which tools to use and when can be more daunting than implementing the tool itself. At other times, the problem is so big that is difficult to know where to start!
Kallion’s diagnostic approach can be tailored to virtually any kind of laboratories. Kallion can not only help identify the (lean) waste but can also assist in quantifying its impact and therefore help prioritize corrective and preventive actions. The consulting support offered by Kallion can further be customized to assist the laboratory with the successful and sustained roll-out of these actions. Please reach out for an initial discussion on how Kallion can assist you.